Products List
-
big fireclay bottom blocks
Description: Using big vibrating table and adopting special castables, the company produces furnace l...
-
fire clay bricks
Description Fireclay bricks are the most widely used refractories made from clay minerals. It can be ...
Refractory Knowledge
-
The High Temperature Operation and Maintenance Guideline of C
Ceramic fiber products have good high temperature resistance, fire resistance, resistance to oil, aci...
-
The firing temperature of the high alumina brick depends on t
The firing temperature of the high alumina brick depends on the sintering properties of the alumina r...
-
Thermal Shock Resistant Fireproof Heat Insulating Brick
Ceramic roller kiln is a new type of energy-saving kiln widely used in recent years with thousands of...
-
Introduction to the performance of clay bricks
Introduction to the performance of clay bricks...
News Center
-
A Brief Analysis of Boiler Masonry and Its Function
Generally, small boilers are installed quickly and do not need to be built on site. For power plant b...
-
Factory Directly Supply With Popular Refractory Bricks in Ch
The use of kilns is inseparable from refractory bricks, but if the details of refractory bricks are n...
The Seven Steps of Fire Clay Brick Production
1. Take earth. The soil bake brick uses taking from two feet deep of the ancient soil under the earth's surface. The layer of soil color is slightly deeper than the overburden,it formed in eighty
thousand to about eighty thousand years ago. At that time, the earth's climate is warm and moist, rich biological role makes this period of the formative soil soft and sticky, is good material of fire
brick.
2. Dig out of clay, in the process of passing about half a year of open air accumulation, let sunshine illuminate, snow and rain frozen erosion, make its internal decompose and loose, then by
manual crushing, sieving, leaving only fine pure soil.
3. Add water into pour soil, make it moist, and then repeatedly refine, or use the cow power trample, make it become thick mud, human through mud and refine need five to six times, the process
play a crucial role in the quality of the brick.
4. Fill soil into wooden blocking mode, after compaction, use iron wire to scrape off the excess sludge and become blank shape. Before blocking, need to sprinkle a layer of fine sand under
wooden underground, in case of mud and ground adhesion.
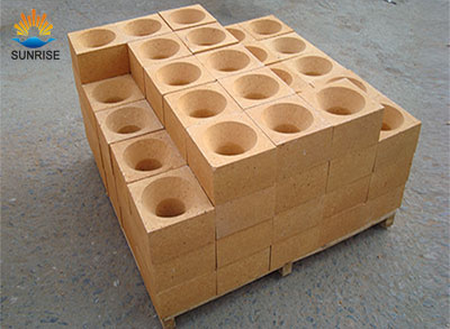
5.. After stripping the brick, need to place sun back to dry in the shade, to prevent exposure to make brick bad and appear crack and deformation.
6. After waiting for adobe completely dry (about one to two months), then into the kiln, the process is one of the most important link in the whole process of brick, common brick uses coal as fuel,
while compactness higher feed slurry brick uses wheatgrass, pine slowly burn, etc.
7. By ten days of fire, green body has been sintered basically, if shut down slowly at this moment, the outside air enters into the furnace, after cooling the body, appeared red, this is our common
red brick, black brick should turn to rust in the stove, the way is when the high temperature sintered bricks, use mud to seal kiln top air holes, reduce air admission, make the temperature in
furnace into reducing atmosphere, in order to prevent the oxidation of the low iron in the green body, on the kiln top of the sealed iron water, make water encounter high temperature, and become
steam, absorb heat quantity in furnace, in the cooling process of furnace body, continue to keep reduction atmosphere, until completely cooling, take out of the kiln. The process of from loess to
the black brick is completed.
If you have any needs our help or are interested in our products, you can click online advisorychat with us online, or call our customer service telephone: 0086-0371-63838939. We will sincerely serve for you!