Products List
-
big fireclay bottom blocks
Description: Using big vibrating table and adopting special castables, the company produces furnace l...
-
fire clay bricks
Description Fireclay bricks are the most widely used refractories made from clay minerals. It can be ...
Refractory Knowledge
-
Thermal Shock Resistant Fireproof Heat Insulating Brick
Ceramic roller kiln is a new type of energy-saving kiln widely used in recent years with thousands of...
-
The High Temperature Operation and Maintenance Guideline of C
Ceramic fiber products have good high temperature resistance, fire resistance, resistance to oil, aci...
-
The firing temperature of the high alumina brick depends on t
The firing temperature of the high alumina brick depends on the sintering properties of the alumina r...
-
Introduction to the performance of clay bricks
Introduction to the performance of clay bricks...
News Center
-
A Brief Analysis of Boiler Masonry and Its Function
Generally, small boilers are installed quickly and do not need to be built on site. For power plant b...
-
Factory Directly Supply With Popular Refractory Bricks in Ch
The use of kilns is inseparable from refractory bricks, but if the details of refractory bricks are n...
How can we improve the production quality of high alumina brick
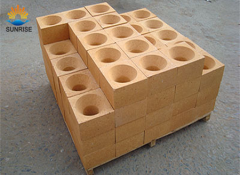
If you have any needs our help or are interested in our products, you can click online advisorychat with us online, or call our customer service telephone: 0086-0371-63838939. We will sincerely serve for you!